Blue Pottery – The Timeless Craft of Jaipur
- Siddhi Prada
- Mar 10
- 4 min read
1. Name & Origin
Blue Pottery is a traditional craft of Jaipur, Rajasthan, known for its striking cobalt blue designs on a glazed, non-clay base. Unlike conventional pottery, blue pottery is made from quartz stone powder, powdered glass, and natural gum, giving it a distinctive smooth and glossy texture.
The origins of blue pottery can be traced back to Persia, Central Asia, and China, where Mongol artisans developed the technique of blue glaze on ceramics. This art traveled to India in the 14th century through Turkic invasions and was later refined under the Mughal and Rajput rulers. Jaipur’s royal patronage, particularly under Sawai Ram Singh II (1835–1880), transformed blue pottery into an iconic craft of Rajasthan.
In 2006, Jaipur Blue Pottery was granted the Geographical Indication (GI) tag, ensuring its authenticity and promoting artisan welfare.

2. Unique Features
Jaipur’s blue pottery stands out due to its vibrant hues, Persian-inspired motifs, and delicate craftsmanship.
Key Features:
Non-Clay Composition – Made from quartz powder, powdered glass, Multani mitti (Fuller’s earth), and borax instead of clay.
Low-Fired & Glazed – The pottery is fired at low temperatures, making it delicate but highly decorative.
Bright Blue & Green Tones – Cobalt oxide gives the pottery its iconic blue shade, while copper oxide adds green hues.
Hand-Painted Motifs – Designs feature floral patterns, birds, animals, and geometric shapes, inspired by Persian and Rajasthani art.
Utility & Decorative Appeal – Blue pottery is used to make tiles, vases, bowls, plates, coasters, knobs, and home décor items.
3. Making Process
Creating blue pottery is a labor-intensive process, requiring precision and multiple stages of craftsmanship.
Step 1: Preparing the Dough
Quartz stone powder, powdered glass, borax, gum, and Multani mitti are mixed with water to form a soft dough.
The dough is left to rest for two days before shaping.
Step 2: Molding & Shaping
The dough is rolled out and pressed into molds made of Plaster of Paris (POP).
The shaped pieces are left to dry for 1–2 days.
Step 3: Designing & Painting
The dried surface is polished with sandpaper for a smooth finish.
Artists use squirrel hair brushes to paint intricate designs with cobalt oxide and natural dyes.
Step 4: Glazing & Firing
A glaze mixture made from powdered glass, zinc oxide, and boric acid is applied.
The pieces are fired in a kiln for 4–5 hours at 800–1000°C.
The final product emerges with a glossy, vibrant finish.
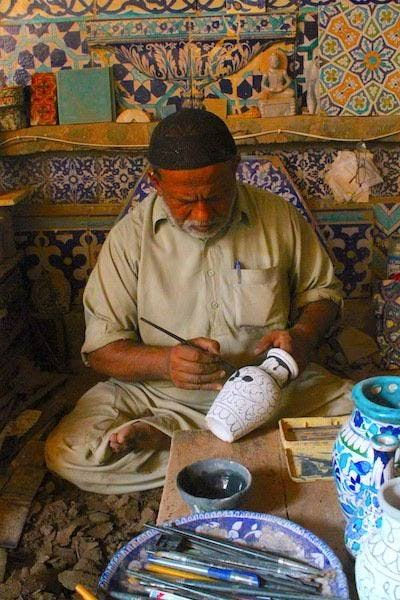
4. Role in Regional Tourism & Exports
Jaipur’s blue pottery is a major attraction for tourists and plays a significant role in Rajasthan’s handicraft industry and exports.
Economic Impact - Over 500 artisans are engaged in blue pottery production across Jaipur, Sanganer, and Neota. The industry generates an annual turnover of ₹50–100 crore, with increasing demand in India and abroad. Exports to the USA, UK, and Europe have grown due to rising global appreciation for handmade crafts.
Tourism & Cultural Influence: Jaipur Blue Pottery is prominently displayed in museums, luxury hotels, and heritage sites such as the Rambagh Palace and City Palace. Tourists frequently visit Jaipur’s blue pottery workshops, with interactive sessions and live demonstrations. The Rajasthan government promotes blue pottery through craft fairs, boosting local artisan recognition.
5. How to Identify Authentic Blue Pottery
Non-Clay Base – Genuine Jaipur Blue Pottery is made of quartz, glass powder, and gum, not clay.
Vibrant Hand-Painted Motifs – Authentic pieces display Persian floral designs, birds, and geometric shapes.
Bright Blue & Green Hues – Colors derived from cobalt and copper oxides create the signature look.
Smooth & Glazed Finish – The surface should be glossy and non-porous, with no visible cracks.
GI Tag Certification – Look for Jaipur Blue Pottery GI tags or authentic artisan labels.
6. Challenges
Despite its popularity, Jaipur Blue Pottery faces several challenges:
Fragility – Since blue pottery is low-fired, it is more delicate and breakable than traditional ceramics.
Imitation Products – Mass-produced, machine-made imitations from other regions threaten the authenticity of Jaipur’s artisans.
High Production Costs – The handmade process and natural dyes make blue pottery expensive compared to machine-printed ceramics.
Declining Artisan Numbers – Younger generations are hesitant to continue the craft due to financial instability.
7. Fun Facts
The Rambagh Palace in Jaipur features blue pottery tiles in its fountains and interior décor.
Jaipur Blue Pottery was revived in the 1950s by painter Kripal Singh Shekhawat, with support from Maharani Gayatri Devi.
The Maharaja Sawai Ram Singh II introduced blue pottery to Jaipur after witnessing Persian artisans in Delhi.
Unlike traditional ceramics, blue pottery does not develop cracks, making it hygienic and water-resistant.
Blue pottery designs were historically inspired by Persian tilework but evolved to incorporate Indian floral and bird motifs.
References -
Geographical Indications Journal, ‘Jaipur Blue Pottery’ (2006) GI Application No. 100, Controller General of Patents, Designs, and Trademarks (India).
Government of Rajasthan, Jaipur Blue Pottery: A Heritage Craft, Rajasthan Tourism Department (2021).
Krishna Shekhawat, The Revival of Blue Pottery in Jaipur (Jaipur Arts Press 2010).
Rajesh Kochhar, Ceramic Heritage of India: From Persian Influence to Local Artisans(Cambridge University Press 2015).
Arundhati Dasgupta, ‘Traditional Indian Pottery: Evolution and Market Challenges’ (2018) 34(2) Journal of Indian Handicrafts Studies 45.
Rajasthan Tourism, ‘Blue Pottery: Jaipur’s Legacy in Ceramics’ (Incredible India, 12 March 2022) https://www.incredibleindia.org accessed 24 February 2025.
Ministry of Textiles (India), ‘Handicrafts Promotion and Blue Pottery’ (Government of India, 2021) https://www.handicrafts.nic.in accessed 24 February 2025.
UNESCO, ‘Blue Pottery: Intangible Cultural Heritage of Rajasthan’ (UNESCO India Report, 2020) https://www.unesco.org accessed 24 February 2025.
Kommentare